Safety and Health Initiatives
Related SDGs
Frequency rate of lost work time due to work-related accidents (Years) and Ratio of work-related accidents resulting in lost work time by 1,000 persons (Years)
We aim to ensure the safety and health of workers in the workplace and create a comfortable work environment.
- Frequency rate of lost work time due to work-related accidents (Years)
-
FY 3/2025
1.41
- Ratio of work-related accidents resulting in lost work time by 1,000 persons (Years)
-
FY 3/2025
1.36
01Basic View
We recognize that ensuring the safety and health of workers in the workplace and creating a comfortable working environment are key management issues. In accordance with the Occupational Safety and Health Policy, the Nisso Group aims to reduce management risks and improve employment opportunities for the working people by clarifying systems and continuing to build, implement, and improve management and activity systems.
02Nisso Group Occupational Safety and Health Policy
The Nisso Group’s occupational safety and health activities are the foundation of our corporate management, and ensuring the safety and health of all workers working at the Nisso Group has become our utmost priority. By establishing a comfortable work environment, and by unifying the entire company to work together in all aspects of our business activities, we will strive to actively promote and improve our occupational safety and health activities, and will continue to aim for a true zero disaster workplace.
- In all aspects of our business activities, we will strive to prevent workplace accidents and disasters by taking the necessary measures to eliminate or reduce risks based on the investigations of dangers and hazards and the results thereof.
- We will develop safety and health activities with the participation and cooperation of all employees and relevant parties of the Nisso Group, and will continue to aim for the improvement of our safety and health standards.
- In addition to complying with the Industrial Safety and Health Act, relevant laws and regulations, and the health and safety regulations established at the workplace, we will endeavor to improve the level of our safety and health management by establishing, periodically reviewing, and continuously enhancing our occupational safety and health management structure.
- In order to prevent health problems caused by overwork and mental health, we will promote the maintenance of health of all employees by reducing excessive working hours and enhancing our health management structure.
- We will promote measures to prevent traffic accidents, and will raise awareness in order to ensure both vehicular and pedestrian traffic safety.
- We will conduct education and training necessary to ensure the safety and health of all employees, and will improve their knowledge and awareness regarding safety and health.
- We will ensure the full dissemination of the Nisso Group’s Occupational Safety and Health Policy to all employees, and will continue to aim for zero accidents and disasters in the workplace.
Occupational Safety and Health Management
In order to manage the safety and health of our company, the Nisso Group has established a company-wide Safety and Health Committee and a safety and health committee for each business site, and holds a meeting once a month for each committee to deliberate and share information on the prevention of occupational accidents and health problems. In addition, in order to ensure the safety and health of all working people, we have introduced an occupational safety and health management system, formulated a company-wide action plan to achieve zero occupational・traffic accidents, and are promoting the PDCA (Plan, Do, Check, Act) cycle of safety and health activities.
Unique "Occupational Safety and Health Management System"
Pplanning
- Declaration of safety and health policy
- Setting of safety and health goals for each business site and workplace
- Establishment of workplace safety and health system, and formulation of workplace rules
- Creation of safety and health plan
DImplementation・inspection・improvement of health and safety plan
- Risk assessments, workplace inspections, hiyari hatto, etc.
CProgress confirmation
- Reporting, confirmation, deliberation, and recording at the Safety and Health Committee
- Investigation of causes of occupational accidents, etc.
ACorrective action
- Reflection of activities in safety and health activity reports
- Preparation of safety and health activity report
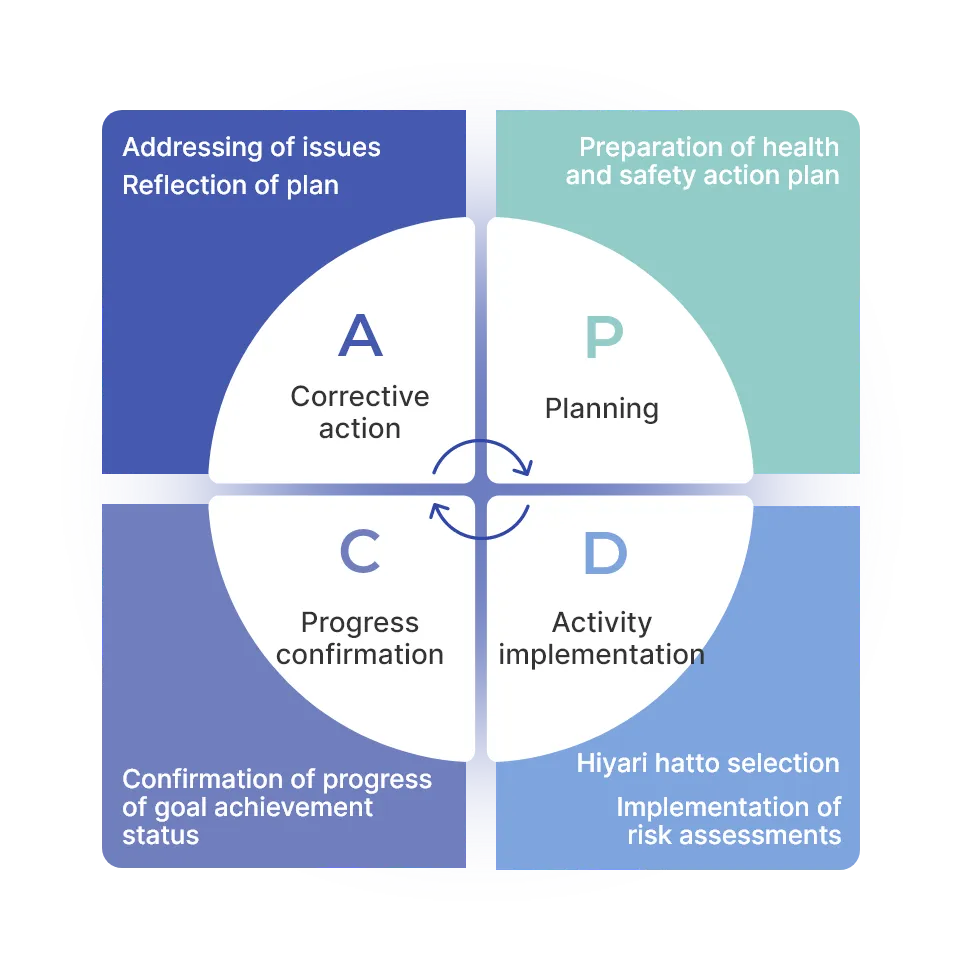
03Occupational Safety Activities
Based on the Occupational Safety and Health Policy, we formulate one-year activity plans and carry out safety and health activities.
Promotion of Annual Plans based on Safety and Health Management Structure
National Safety Week
We held the "National Safety Week" for the purpose of preventing occupational accidents. During the implementation period from July 1 to July 7, 2023, we notified employees of the contents of our occupational accident prevention activities, and worked to improve safety activities and safety awareness.
Slogan
-
Raising awareness and safety behavior Let‘s build a zero-disaster workplace for everyone
Main priority items
-
- Measures to prevent machinery-related accidents and falls
- Measures to promote voluntary safety and health activities
- Measures to prevent traffic accidents etc.
Year-end and New Year "Zero Accident" Campaign
The period from December 1, 2022 to January 15, 2023 was carried out as the "Year-end and New Year Zero Accident Campaign". Based on the notification and implementation guidelines of the Ministry of Health, Labour and Welfare, we shared priority implementation items and worked on safety activities in order to achieve zero-accidents and zero-disasters.
Measures for Hazard Prevention
Risk Assessments
Based on our annual plans, we conduct risk assessment activities in advance at our workplaces in order to prevent hazards. We conduct more thorough activities at sites where we manage chemical substances.
Workplace Inspections
We reduce risks by promoting safety guidance and improvements by conducting workplace inspections (at all workplaces) by health officers and workplace inspections by industrial physicians (at locations of 50 or more people).
Hiyari Hatto (near-miss reporting) Activities
In order to identify potential risks in the workplace and prevent disasters in advance, we report and improve hiyari hatto activities.
Safety and Health Education
Hazard Simulation Education
Nisso Technical Centers (TCs), which are training facilities owned by NISSO HOLDINGS in 9 locations nationwide, are furnished with equipment that simulate hazards, and education with real-world experiences are provided.
KYT (Kiken Yochi Training, or Hazard Prediction Training)
KYT is implemented as a voluntary activity. By raising our sensitivity to hazards and applying them to risk assessment practices, we are able to create a safer workplace environment.
Safety and Health Study Groups
We hold study group sessions aimed at promoting safety and health activities and acquiring knowledge of laws and regulations. We will further raise safety and health standards by raising safety awareness among all employees involved in the promotion activities, including safety personnel.
Traffic Safety Initiatives
Accident Prevention Activities
We are taking various measures to prevent traffic accidents, such as having our staff take courses at driving schools, utilizing analysis results by obtaining driving record certificates, enforcing parking rules and conducting quarterly checks, installing drive recorders in new vehicles and conducting video checks, creating traffic warning maps, conducting on-board passenger checks, having our staff watch traffic safety videos, implementing traffic KYT, and thoroughly implementing vehicle 4S. In addition, in order to raise awareness of safe driving, we continuously conduct traffic safety patrol activities at the gates and parking lots of our clients' factories.
Disaster Prevention Initiatives
Disaster Prevention Activities
We conduct regular disaster prevention drills at workplaces, provide guidance and education for fire prevention, and conduct inspections of employee dormitories, etc.
04Promotion of Occupational Health Management
The Nisso Group places top priority on the health of our employees. In order to ensure their health, we promote work environment management, work management and health management, which are the fundamentals of occupational health management. At the same time, we promote the creation of a workplace environment where employees can work for a long time in good physical and mental health.
Health and Occupational Health Management Initiatives
Appropriate management of working hours to control long working hours
In order to control long working hours, we have established our own rules to prevent overwork by providing interview guidance by doctors in accordance with the requirements for overtime work hours.
Various health examinations
We carry out various health examinations (general and special health examinations, etc.) to help maintain and improve the health of workers by listening to opinions from doctors based on the results, and recommending re-examinations.
Heatstroke prevention measures
From May to September 2023, we implemented measures to prevent heatstroke among employees by distributing salt candy and proposing environmental improvements at workplaces with the goal of zero heatstroke occurrences.
National Occupational Health Week
We held "National Occupational Health Week" with the aim of preventing health disorders. During the implementation period from October 1 to October 7, 2023, we notified employees of the contents of our activities to prevent health problems and worked to improve health management and the workplace environment.
Slogan
-
Let's aim to be two-way A healthy workplace for mind and body
Main Priority Items
-
- Prevention of health problems caused by chemical substances (Implementation of risk assessments)
- Promotion of mental health care
- Securement of worker safety and utilization of safety confirmation system
05Measures to Prevent Health Problems
Health problem prevention activities and management
Based on our annual plan, we are implementing activities to prevent health problems caused by heat stroke, infectious diseases, and lower back pain. In addition, as activities to prevent health problems caused by chemical substances, we implement risk assessments, improve the workplace environment and work methods, and carry out activities to maintain a comfortable workplace, such as wearing appropriate protective equipment.
Mental Health
NISSO HOLDINGS carries out mental health activities not only for physical health but also for mental health promotion. We provide regular mental health education (self-care and "line care", or employee care overseen by managers), and have established an in-house "mental care consultation room" to provide counseling and awareness-raising activities related to mental health In addition, we conduct stress checks once a year for our employees, recommend doctor interview guidance to people with high levels of stress, and make efforts to improve work environments based on organizational analysis.